Cast film extrusion process pdf
He has twenty-three patents to his name and is the editor of Journal of Plastic Film and Sheeting and editor or co-editor of four books on extrusion and packaging. John is a Fellow of the Society of Plastics Engineers and serves on the Extrusion Division and Flexible Plastics Packaging Division boards.
The blown film, cast film and extrusion coating and lamination processes are described with illustrations and markets served. The references provide more detailed explanations for those interested in a more complete understanding of the process and operating parameters.
BFI 8473 Cast P/P Film Properties. Polypropylene 8473 is a low melting, high ethylene random copolymer with improved color, optics and impact properties.
Introduction . Blown film extrusion is a technology that is the most common method to make plastic W films, especially for the packaging industry. The process involves extruding a tube of molten polymer W through a die and inflating to several times its initial diameter to form a thin film bubble.
in Portable Document Format (PDF). POLYETHYLENE FILM EXTRUSION A PROCESS MANUAL. The process involves extrusion of a plastic through a circular die, followed by Industry packaging (e.g.
Download blown film extrusion or read online here in PDF or EPUB. Please click button to get blown film extrusion book now. All books are in clear copy here, …
cast film extrusion process Mon, 24 Dec 2018 16:16:00 GMT cast film extrusion process pdf – Introduction . Blown film extrusion is a technology that is the most
Extrusion I Cast & Blow Film Lines I Quality Control R & D, QC, Lab & on-line application The solution for the polymer & petrochemical industries The original by OCS. The measuring extruder of the type ME is intended for the production of narrow films for laboratory and small-batch production. The optimum simu-lation of the production process is ensured be-cause of the flexibility and the
The cast co-extrusion process combines different polymers into one film in order to benefit from their different mechanical and physical strengths. This is accomplished by feeding multiple extruders into a …
A short review of the extrusion process implies the understanding of the functional zones. The functional zones of a conventional single screw extruder are shown in Fig.1.1.: feed hopper, this zone is designed to operate under gravity flow and it feeds the granules or the particulate solids into the extruder, solids conveying zone,thiszone isdesignedtotransport andtoslightly compressthe gran
4/08/2016 · Working of extruder blown film plant is shown with the help of animation.
Abstract In cast film extrusion, the polymer melt is extruded through a slit die, slightly stretched in air and then cooled on a chill-roll. An important part of the present work was devoted to the development and application of a thermomechanical model of stretching in air and of a purely thermal model of cooling on the roll, taking polymer
YouTube Embed: No video/playlist ID has been supplied
Cast Film Line Cast Film Extrusion Machine Plastemart

Coating extrusion line All industrial manufacturers
A BASIC EXPERIMENTAL STUDY OF CAST FILM EXTRUSION PROCESS FOR FABRICATION OF PLASTIC MICROLENS ARRAY DEVICE Chih-Yuan Chang and Yi-Min Hsieh and Xuan-Hao Hsu
Cast Film Processing Guide for VERSIFY™ Plastomers and Elastomers When processing VERSIFY™ Plastomers and Elastomers in cast film applications, it is very important to always start with a clean extrusion system: • Completely purge other polymers from the system prior to collecting good film • Make sure all die surfaces are clean and free of buildup • Change screen packs just prior to
extrusion conditions may vary from 102 Pa s to 105 Pa s. The shear stress is measured in units of is to force polymers to flow through dies and process equipment. During single-screw extrusion, shear rates may reach 200 s–1 in the screw channel near the barrel wall, and much higher between the flight tips and the barrel. At the lip of the die the shear rate can be as high as 1000 s–1
Page 1 of 2 Troubleshooting Guide for Cast Film and Sheet Extrusion Problem Possible Causes Possible Solutions 1. Applesauce, gels, poor clarity
Complete single layer and multi-layer film solutions for the production of technical packaging film, for application in food and medical-pharmacological fields, agrifilm, biodegradable film and thick film for geomembranes intended for civil and industrial waterproofing systems.
In the cast film extrusion process, the molten polymer travels through a flat die system to adopt its final flat film shape. The die system is formed by the die and feedblock (if the process requires coextrusion) or simply the die, if the process is that of mono-layer extrusion.
The majority of new equipment being installed for both blown and cast film extrusion will be capable of coextrusion. The shift to coextrusion is being made because the technology can meet a wide range of application needs, including the ability to achieve specific performance properties, to reduce costs, to use fewer processes and to reduce waste source. The advances in coextrusion equipment
MDO* is a proven technology which saves resources, improves film properties, and optimizes films for specific uses. With MDO from W&H, both cast and blown film can be stretched monoaxially. The process improves barrier properties and gives mono and coextruded films enhanced tensile strength and stiffness, better shrink properties, and increased gloss and transparency.
COEXTRUDED MULTILAYER FILM CONTENTS SECTION I PRODUCT CHARACTERISTICS 1. Cast film extrusion 2. Blown film coextrusion 3. Co-extrusion coating 4. Co-extrusion lamination In cast coextrusion method, each material is fed by individual extruders to a flat die. The materials are combined within the die to form a multilayered melt which extrudes through the die to form a flat film …

Information About the Training This 2-day course is intended to give the participants a good understanding of the Blown Film Extrusion process.
17/01/2013 · Animation of extrusion of LDPE film and shrinking on a 6 x PET bottles and closed cycle at the end.
Find your coating extrusion line easily amongst the 21 products from the leading brands on DirectIndustry, the industry specialist for your professional purchases.
16 CHAPTER 04 FILM BLOWING Prior to analysis of poly bag manufacturing process, it is essential to have a better understanding of the key manufacturing process- the film blowing.
Cast Film Technology for Processing of Recycled PET PET Recycling Forum 2008, Moscow, 12th February 2008 Dr. Stefan Hoffmann
Evolution extrusion line. During the demonstrations, the new FFC ultralight composite is extruded as a skirting profile, which is the best compromise between the need to show the full characteristics and potentials of this new material and the constraints imposed by an exhibition setting. The line exhibited at the fair is equipped with an Omega single-screw extruder, which processes a dryblend
In the cast film extrusion process, the melt is extruded through a wide die as a thin web and is cooled on a polished metal casting roll. Raytek point sensors help control
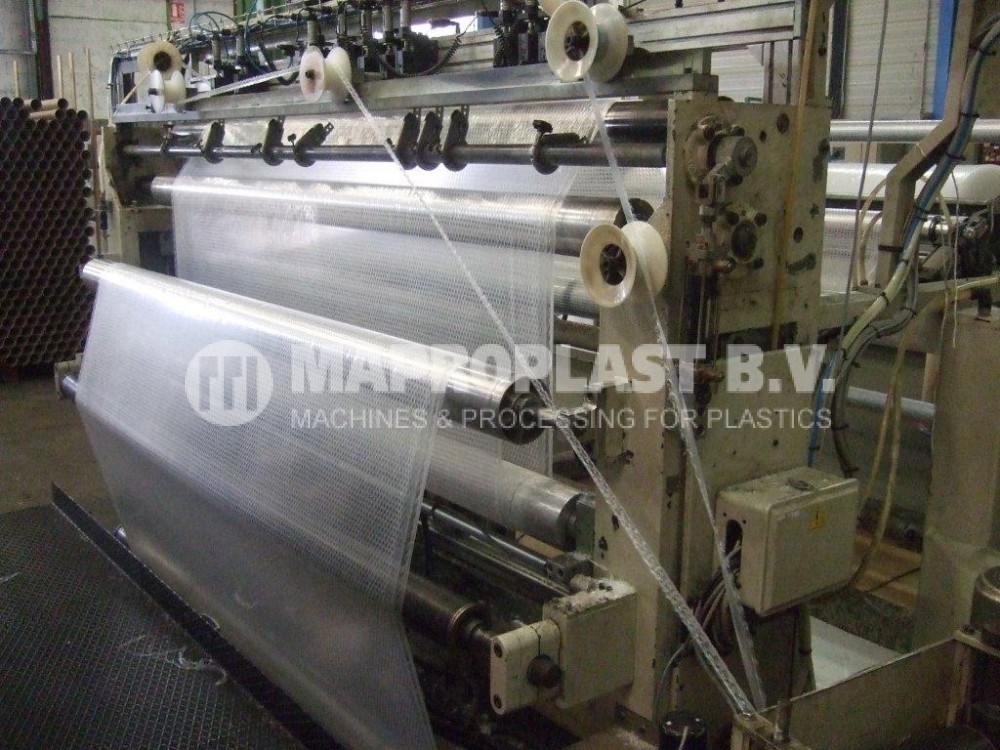
Manufacturers of cast film lines, cast sheet extrusion machinery, cast film extruders and cast film extrusion machines. Source cast film machine, CPP film line, cast PP sheet line, cast film extruders and cast film line.
Dynamic Modeling of Blown-Film Extrusion H+ Fig. 1. Schematic of blown Jzh extrusion a circumferential tension on the bubble-tube. The re- sulting biaxial stress can further induce crystalliza-
Process • Reduce film tension • Reduce film temperature • Eliminate affect of air currents Equipment • Reduce drag resistance in collapsing frame • Reduce drag resistance in bubble cage • Match rotation speed of rollers to line speed • Reduce width of spreader roller grooves • Adjust position of spreader roller • Reduce idler roller deflection • Reduce drag resistance
The cast film process can run resins with low melt strength, (typically higher melt index) whereas the blown film process requires those with higher melt strength. LLDPE is an exception here and must be modified to prevent drawdown resonance.
Whether your fabrication process includes blown film, BOPE (bi-oriented Polyethylene) film, Bi-Oriented Polypropylene (BOPP) film and cast film, you can count on Dow’s expert capabilities for technical, process or design issues.
Film is divided into two subcategories: cast, or flat film; and blown film. In the former, hot plastic is extruded through a flat, slit die onto a polished chill roll where it is quenched, pulled to a second set of rolls to cool the other side, then wound. In blown film, plastic is extruded into a
processing parameters in extrusion process. Therefore, determining the effect of processing parameters and process conditions in cast film extrusion is important to obtain the exact properties of the films for their end uses. Cast film technology is the simplest technology to produce polymeric films in which the molten polymer is extruded through a slot die, fed by a single-screw extruder
A Basic Experimental Study of Cast Film Extrusion Process
• Preheated billet will develop an abrasive oxide film that These parts may also be made by casting, forging, or machining; process choice depends on the dimensions and the materials involved and on the properties desired. Economic considerations are also important in final process selection. (b) and (c) Impact extrusion of a collapsible tube by the Hooker process. Hydrostatic Extrusion
Principal Lecturer Paul Waller has been involved in the plastic film industry . for more than 30 years. Clients have included raw material suppliers, processors, end …
Process: Sheet and Cast Film extrusion SAFETY FIRST: Before performing any procedure, it is the machine operator’s responsibility to be aware of their company’s safety policy, to wear the appropriate personal protective equipment, and to make sure that only authorized personnel are in the area. PROCEDURE: 1. Maintain temperature and RPM settings for resident resin. 2. Disconnect or shut
lamination cast-film/ substrate layer adhesive solvent or solventless sealing layer multi layer film 0006e .Production techniques solvent and solventless adhesive . C`therm XX HV PE PE (I) ready blown film PE castco-extrusion and sandwichcoating e.g..g.
COMPLETE BLOWN FILM SOLUTIONS Complete Blown Film Solutions TECHNOLOGY PARTNERS Gravimetric Blending & Extrusion Control Automatic Bubble Profile Control Bubble Stabilization & Frost Line Control. COMPLETE BLOWN FILM SOLUTIONS www.tsm-controls.com There are many challenges facing Blown Film producers including energy and material costs, waste & scrap reduc – …
the extrusion process if one does not know the special characteristics of the mate-rial to be extruded. Understanding just the extrusion machinery is not enough. Rheological and thermal properties of a polymer determine, to a large extent, the characteristics of the extrusion process. The process engineer, therefore, should be a mechanical or chemical engineer on the one hand, and a rheologist – film lighting techniques pdf free download cast film extrusion process pdf. blown film extrusion troubleshooting. blown film extrusion process animationextrusion the definitive processing guide and handbook pdf free download. blown film extrusion formulas. blown film extrusion process pdf. The Film Extrusion Manual, Second Edition focuses on the technology and science of polymer film extrusion. The material in this book’s 42 …
Alpha Marathon Film Extrusion Technologies Inc. is a world class leader in the plastic film and extrusion equipment industry. Whether your end product is a monolayer film, stretch or shrink film or an advanced multi-layer barrier structure, Alpha Marathon has the perfect production solution for every possible application including:
Blown Film Extrusion (Dr. Kirk Cantor) About the Seminar This two-day program provides a broad overview of blown film extrusion, including materials,
The cast film process involves the extrusion of polymers melted through a slot or flat die to form a thin, molten sheet or film. This film is “pinned” to the surface of a chill roll (typically water-cooled and chrome-plated) by a blast of air from an air knife or vacuum box.
Extensive information about optimizing the film extrusion manufacturing process, including primary and auxiliary equipment used in the process.
For extrusion coating, only one substrate is used and the extrudate coats the surface and is quenched on a chill roll much like a cast film process. The various products that are typically made with extrusion coating and laminations include lidding stock, …
The optimized dsX s-tretch™ pre-stretch cast film extrusion line is the first in-line pre-stretch system enabling customers to run thinner films at higher speeds. This line enables stretch film providers to produce consistent, high-quality pre-stretch film with greater efficiency. The two-meter wide line also has the advantage of a smaller footprint, yet allows for growth.
Different types of dies used for blown film extrusion. Adapted from W. Michaeli, Extrusion Dies for Plastics and Rubber, 2 nd Edition, Hanser Publishers, Munich, Germany, 1992 [6]
Single and multi-layer plastic film products are often obtained by flat cast extrusion. This technology is specifically suited for the production of food packaging and technical films,
3 FILM EXTRUSION AND CONVERSION 2 Qenos Technical Guides TABLE OF CONTENTS PART A. FILM EXTRUSION 6 GRADE SELECTION FOR FILM EXTRUSION 6 Comparison of Product Types and Classes 6 Blending of LLDPE, mLLDPE and LDPE 7 Blending of HDPE with LLDPE and LDPE 8 Coextrusion 8 FILM EXTRUSION TECHNOLOGY 8 Process Description 8 Blown Film Parameters 9 …
WPA Conference Newport Beach, CA June 21-23, 2016 Nick Nigro Sales Product Manager Extrusion – North America The Effects of Process and Cooling on Film Properties
Cover extrusion (“cross heading”) 15 Cast film, sheeting and fabric coating 16 Blown film 19 Lay-flat hose liner extrusion 19 Co-extrusion 20 Troubleshooting Guide 22 Table of Contents Hytrel® Thermoplastic Polyester Elastomer Hytrel® thermoplastic polyester elastomers are block copolymers, consisting of a hard (crystalline) segment of polybutylene terephthalate and a soft (amorphous
Cast film extrusion is a widely used technique to produce polymer films for packaging or coating applications. The final width of the film may be smaller than the initial die width (necking phenomenon) and therefore is the final film thickness larger than what one could expect.
COMPLETE BLOWN FILM SOLUTIONS TSM
Typical Purge Procedure with DuPont TM LDPE 6611 For Cast Film applications: Description: LDPE . 6611 is a fractional melt index low density polyethylene resin that contains various additives to assist in purging and cleaning the extruder. This polymer is formulated with agents to help it wet and scour metal surfaces within the extrusion system. It also contains a blowing agent which helps to
Some extrusion lines have printing equipment and bag-making machines on-line. Simpler extrusion lines form the film or sheet and then perform the printing and bag-making functions off-line. Coextrusion is a variation of this process. The die is designed with multiple flow channels so that multiple layers may be formed. Multiple layers are typically used in order to protect the product from
PLASTIC FILM MANUFACTURERS PROCESS ASSESSMENTS

Cast Film Extrusion International Polymer Processing
Blown Film Extrusion Download eBook PDF/EPUB
THE EXTRUSION PROCESS UNIDIRECTIONAL FILM hannecard.com
DuPont Hytrel Extrusion Manual
Extrusion I Cast & Blow Film Lines I Quality Control
Extrusion process blown film – animation created by MAYA
– Plastics Industries Fluke Corporation
Who should attend? Principal Lecturer RHEOLOGY AND
hosokawa-alpine.de Blown film lines
YouTube Embed: No video/playlist ID has been supplied
Cast Film Technology for Processing of Recycled PET
Comments
4 responses to “Cast film extrusion process pdf”
The majority of new equipment being installed for both blown and cast film extrusion will be capable of coextrusion. The shift to coextrusion is being made because the technology can meet a wide range of application needs, including the ability to achieve specific performance properties, to reduce costs, to use fewer processes and to reduce waste source. The advances in coextrusion equipment
Alpha Marathon Plastic Film and Extrusion Equipment
Film Extrusion Plastics Technology
CHAPTER 04 FILM BLOWING UoM IR
Extrusion I Cast & Blow Film Lines I Quality Control R & D, QC, Lab & on-line application The solution for the polymer & petrochemical industries The original by OCS. The measuring extruder of the type ME is intended for the production of narrow films for laboratory and small-batch production. The optimum simu-lation of the production process is ensured be-cause of the flexibility and the
Technical Training on Blown Film Extrusion MPMA
Evolution extrusion line. During the demonstrations, the new FFC ultralight composite is extruded as a skirting profile, which is the best compromise between the need to show the full characteristics and potentials of this new material and the constraints imposed by an exhibition setting. The line exhibited at the fair is equipped with an Omega single-screw extruder, which processes a dryblend
Cast Film Extrusion of Polypropylene Films International
Film is divided into two subcategories: cast, or flat film; and blown film. In the former, hot plastic is extruded through a flat, slit die onto a polished chill roll where it is quenched, pulled to a second set of rolls to cool the other side, then wound. In blown film, plastic is extruded into a
MDO Windmoeller & Hoelscher Corporation
Cast Film Technology for Processing of Recycled PET
Cast Film Line Cast Film Extrusion Machine Plastemart